5 Ways to Improve Dispatch Efficiency in Your Warehouse
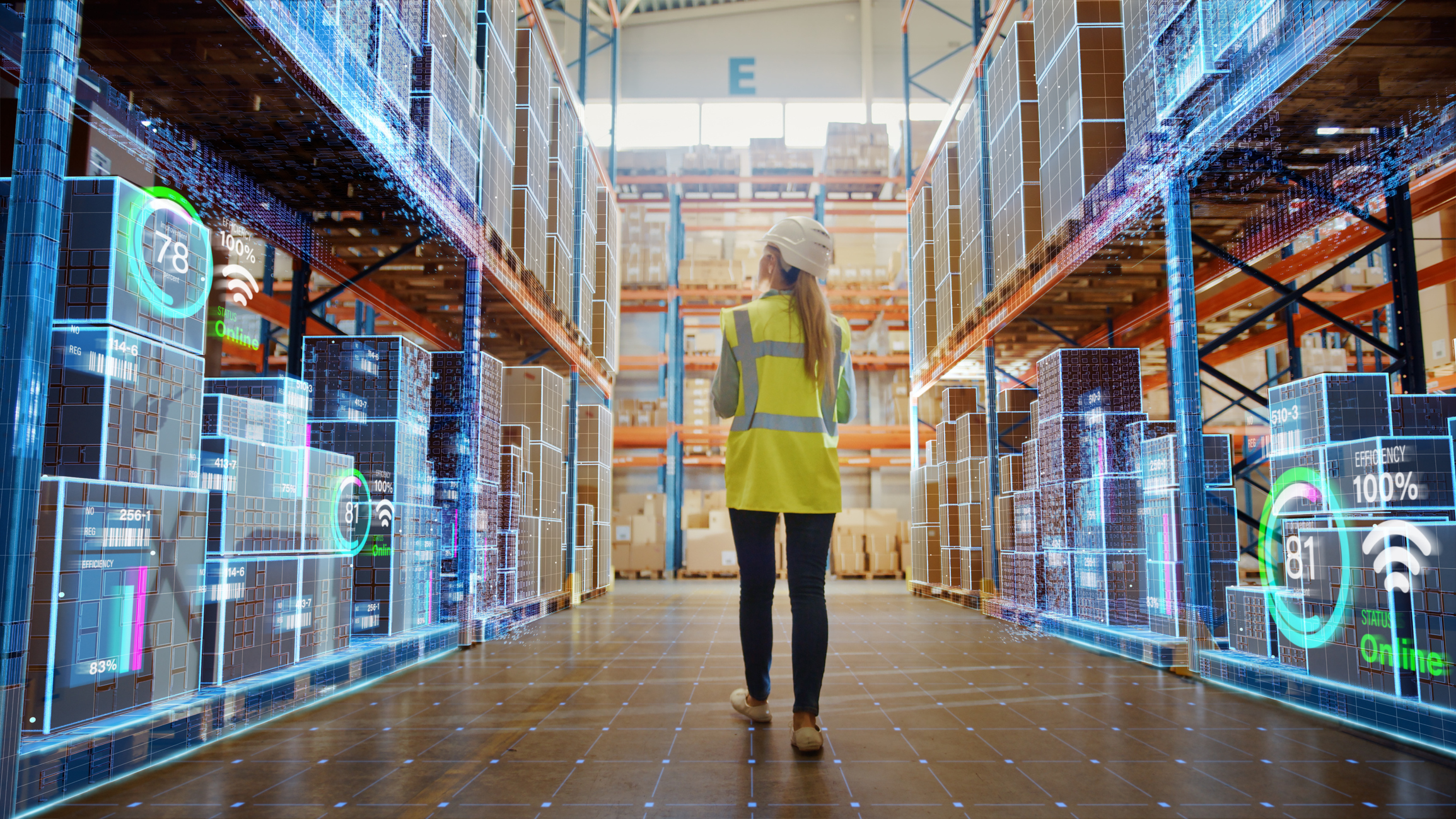
By leveraging Warehouse Management System (WMS) technology, automation, and strategic workflow improvements, you can significantly enhance your warehouse’s dispatch efficiency. Here are five key ways to achieve this:
1. Implement an Advanced Warehouse Management System (WMS)
A WMS is the backbone of an efficient dispatch operation. It provides real-time data on stock levels, order status, and shipment tracking, ensuring your team can process orders accurately and quickly.
With features such as automated order allocation, barcode scanning, and real-time reporting, a WMS eliminates manual errors and speeds up the dispatch process. By integrating a WMS like Optima, businesses can streamline workflows and improve overall operational efficiency.
2. Optimise Picking and Packing Processes
An inefficient picking and packing process can cause major delays in dispatch operations. To improve efficiency:
- Use a zone picking system to reduce travel time for pickers.
- Implement batch picking for bulk orders.
- Utilise barcode scanning to reduce errors and improve accuracy.
- Standardise packing procedures to ensure consistency.
A WMS helps automate these processes by providing optimised picking routes, reducing errors, and enhancing order accuracy.
3. Streamline Shipping and Carrier Integration
Seamless integration with shipping carriers ensures faster dispatch and reduces shipping errors. A WMS can automatically generate shipping labels, track parcels, and select the most cost-effective courier service for each order.
With direct integration to major carriers, you can reduce processing times and enhance order tracking, leading to greater customer satisfaction.
4. Improve Warehouse Layout and Organisation
A well-organised warehouse directly impacts dispatch efficiency. Implement these strategies to reduce time wastage:
- Strategic slotting: Place high-demand items closer to dispatch areas.
- Clear labelling: Use digital labels and barcodes to speed up order picking.
- Defined traffic flow: Designate clear pathways for forklifts and staff to reduce congestion.
By analysing dispatch trends and order volume, a WMS can suggest warehouse layout improvements to optimise workflow.
5. Use Real-Time Data and Analytics
Data-driven decision-making helps identify inefficiencies and streamline processes. A WMS provides valuable insights, such as:
- Average dispatch times
- Error rates in picking and packing
- Carrier performance metrics
By tracking these KPIs, warehouses can continuously refine their dispatch operations for maximum efficiency.
Improve Your Dispatch Efficiency with Optima WMS
At Optima Warehouse Solutions, we provide powerful WMS software designed to enhance warehouse operations, improve dispatch efficiency, and eliminate costly errors.
With real-time stock visibility, automated workflows, and seamless carrier integration, Optima WMS ensures your warehouse operates at peak efficiency.
Get in touch today to learn how Optima WMS can revolutionise your dispatch process!