The 5 Inventory Cost Categories
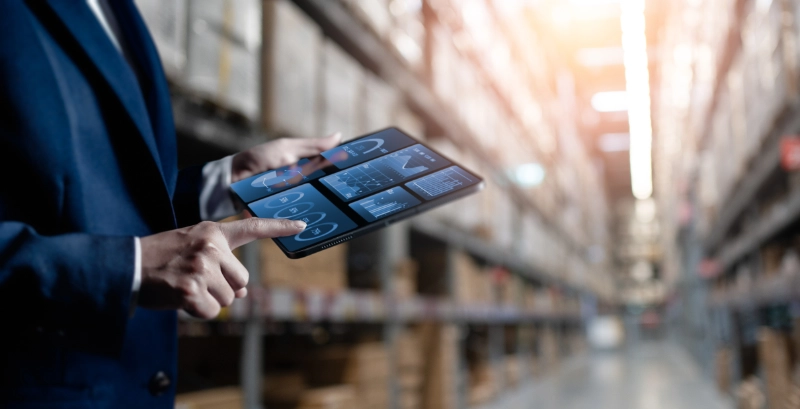
1. Ordering Cost
The Purchase price (including goods and delivery)
The purchase price represents the core cost associated with acquiring goods or services. It encompasses the base cost of the product, along with additional charges such as discounts, rebates, fees for specific services, taxes, duties, and transportation expenses. A comprehensive understanding of these components is essential for effective cost management and profit optimisation.
Staff costs
Staff costs for your buying department represent a significant portion of ordering expenses. This category includes:
Salaries and wages:
Compensation for purchasing department personnel, including buyers, procurement analysts and purchasing assistants.
Overtime pay:
Additional compensation for staff working extended hours to meet deadlines or handle increased workload.
Training costs:
Expenses associated with developing the skills and knowledge of purchasing staff.
Recruitment costs:
Costs incurred in finding and hiring new purchasing personnel.
Indirect labour costs:
Overhead expenses related to purchasing department operations, such as office space, utilities and equipment.
2. Stock Holding Cost
Holding costs, also known as carrying costs, encompass the expenses associated with storing and maintaining inventory until it's sold. These costs can significantly impact profitability and require careful management.
Storage costs
Storage costs encompass the expenses associated with housing and maintaining inventory within a warehouse or storage facility. These costs include the price of the physical space, utilities, maintenance, and the opportunity cost of capital tied up in inventory.
Optimising warehouse layout, implementing efficient storage systems and leveraging technology can significantly impact storage costs. By maximising space utilisation and minimising aisle widths, businesses can reduce the overall square footage required. Additionally, investing in storage solutions like pallet racks, shelving, and automated systems can enhance storage capacity and improve order fulfilment efficiency.
Security costs – staff or security systems
Security costs are essential for safeguarding inventory from loss, damage and theft. These expenses include the implementation and maintenance of security systems, personnel and procedures. Investing in surveillance equipment, access control systems and alarm systems is crucial for deterring theft and detecting unauthorised access.
The cost of protecting your inventory needs to be factored into the total cost of your inventory.
Staff costs
As well as the costs of security staff (and purchasing staff as mentioned above), you also need to account for the costs of your warehouse staff who unload, store, pick, pack, quality control and dispatch your goods.
Other holding costs
Your holding costs also include fees, taxes, insurance and other miscellaneous costs associated with maintaining your stock before it’s sold.
3. Spoilage Costs
Perishing stock
Perishable items, such as fresh produce, dairy products and pharmaceuticals, have a limited shelf life and can become unsalable if not managed effectively. Similarly, technological advancements can render inventory obsolete before it can be sold, resulting in financial losses
Obsolescence
With technology advancing at the rate it is, it’s becoming a real danger that technology may be out of date before you’ve had a chance to sell it. It’s important to only order in quantities that you know you can sell before the next model comes along, else you may be lumbered with outdated stock that you won’t get full price for.
Damage
Damage to inventory is another factor contributing to spoilage and obsolescence costs. Physical damage due to mishandling, transportation or storage conditions can reduce product value or render it unsalable. Implementing robust quality control measures, proper packaging and careful handling practices can help minimise damage and protect inventory investment.
Buying from reputable suppliers who provide proper packaging and handling during transit will also reduce damaged goods, as will training your staff on how to correctly unload and store your stock.
4. Inventory Shrinkage Cost
Theft
While we touched on security costs above, the costs of insufficient security must also be considered. Theft, both internal and external, is a significant contributor to shrinkage.
Lost stock not only represents the loss of a sale but also the loss of the money used to buy the goods in the first place.
Implementing robust security measures, such as surveillance systems, access controls, and employee background checks, can help mitigate this risk.
Supplier error or fraud
Shrinkage can also come from not receiving the correct amount of stock to begin with. Receiving incorrect quantities or damaged goods can disrupt operations and increase costs. Careful supplier selection, clear order documentation and regular audits can help minimise these issues. By implementing effective inventory management practices and addressing potential causes of shrinkage, businesses can reduce losses and protect their bottom line.
5. Stockout Cost
Revenue lost as a result of not having goods in stock
Stockouts result in lost sales opportunities. When a product is unavailable, customers may choose to purchase from a competitor, delay their purchase until the product is restocked or reduce their overall order size. This directly impacts revenue generation and can damage customer loyalty
Why choose Optima WMS?
Reduce inventory costs in your warehouse
Optima WMS can help improve efficiencies and reduce some of your inventory costs. We will automatically track stock volumes, reducing room for manual error and by producing reports and updates, lets you know instantly what needs reordering and how product sales are trending. Automatically reorder low stock
Optima also makes your warehouse staff more efficient by reducing put-away and pick time, this is done by creating optimum routes for your staff to follow through your warehouse.