Warehouse Quality Control.
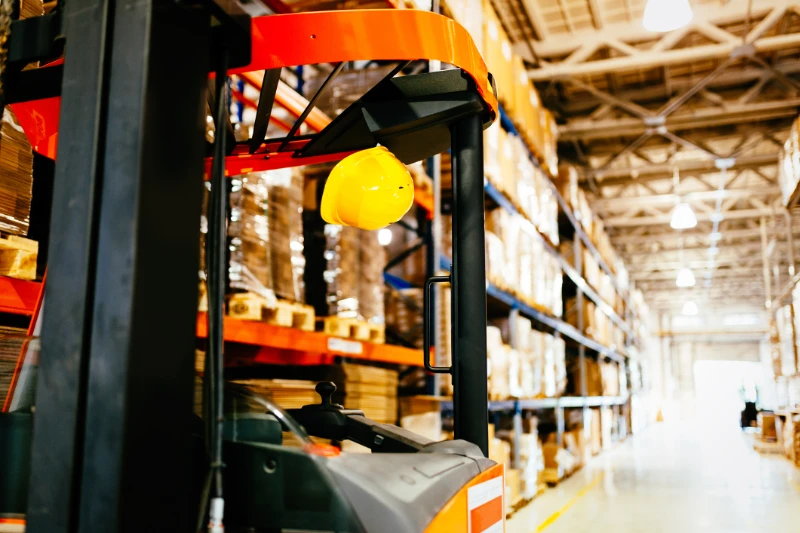
Our 12 Tips for Quality Control in the Warehouse
Effective warehouse quality control is vital for several reasons:
- Maintaining customer satisfaction
- Minimising returns and rework
- Optimising inventory management
- Upholding the reputation of the company.
By implementing robust quality control measures, warehouse managers can enhance efficiency, reduce costs and improve overall operational performance.
Train staff thoroughly
Provide thorough and ongoing training to warehouse staff involved in quality control processes, ensuring they understand the importance of quality control and are proficient in inspection techniques and equipment usage.
Implement regular inspections
Conduct regular inspections of incoming and outgoing goods at multiple points along the supply chain, including receiving, storage, picking and shipping, to identify any defects or discrepancies.
Utilise technology
Invest in technology solutions such as barcode scanners, RFID systems and quality control software to streamline inspection processes, improve accuracy and facilitate data management.
Document everything
Maintain detailed records of all quality control activities, including inspection results, corrective actions taken and communication with suppliers or customers, for traceability and continuous improvement.
Prioritise preventative maintenance
Regularly inspect and maintain warehouse equipment and machinery to prevent malfunctions or breakdowns that could compromise product quality.
Implement FIFO/LIFO systems
Adhere to the principles of First-In-First-Out (FIFO) or Last-In-First-Out (LIFO) inventory management to minimise the risk of product spoilage, expiration or obsolescence.
Establish clear quality standards
Define precise quality standards for all products stored and handled in the warehouse, encompassing specifications for dimensions, appearance, functionality and performance.
Implement cross-checking procedures
Incorporate cross-checking procedures where multiple staff members independently verify product quality to minimise the risk of oversight or error.
Establish contingency plans
Develop contingency plans to address quality issues promptly, including procedures for quarantine, rework or disposal of non-conforming products.
Encourage continuous improvement
Foster a culture of continuous improvement within the warehouse by regularly reviewing quality control processes, soliciting feedback from staff and implementing necessary adjustments.
Train suppliers
Work closely with suppliers to ensure they understand your quality requirements and expectations, providing feedback on any issues encountered and collaborating to address root causes effectively.
Regular audits and reviews
Conduct periodic audits and reviews of quality control processes to identify areas for improvement, ensure compliance with standards and regulations and maintain alignment with organisational goals.
Optima’s role in warehouse quality control
Here at Optima, we specialise in providing innovative solutions for warehouse management and quality control. With advanced features tailored for quality control processes, Optima’s software and technology solutions empower warehouses to streamline workflows, capture real-time data, generate comprehensive reports and improve decision-making and corrective action processes.
By leveraging Optima’s cutting-edge technology, warehouses can achieve higher levels of efficiency, accuracy and compliance in their quality control efforts, ultimately leading to improved customer satisfaction and competitive advantage.